Knowledge update
Pitfalls of automation.
Three pitfalls when automating your warehouse
Automation issue in your warehouse?
Three pitfalls when automating your warehouse.
According to the trade press, speakers at logistics conferences and even according to many logistics managers, you will automate your warehouse. The advantages are obvious: shorter lead times, fewer errors, better use of space, more efficiency and ultimately many satisfied customers.
Reasons for automation.
In general, the consideration to automate is prompted by a number of pain points (busyness and obscurity in the workplace, errors, complaints from staff) or because of a strategic choice (new markets, wanting to deliver faster, more customer satisfaction). The next phase is crucial for the success rate of a project. All processes will have to be looked at very critically, alternatives must be considered and all the pros and cons weighed against each other.
Anyone who is going to invest will therefore do everything in their power to ensure that the implementation is as successful as possible. However, in practice things still regularly go wrong, as a result of which the expensive systems do not do what they have promised. Below we list three pitfalls that should be avoided in an automation or mechanization project.
1. Not taking enough time for the financial calculation.
Except from a logistical point of view, such a project should be viewed primarily from every financial perspective. This is certainly not limited to the investment costs. Operational costs must also be considered so that a true total picture is created. Below this link is an interesting example on logistics.nl.
The right supplier will always point out to the customer both advantages and disadvantages of systems as well as all financial consequences. Only then can a well-considered decision be made and then the starting point is the extent to which the logistics objective is achieved. So take plenty of time for this.
2. The new system has not been sufficiently ‘sold’ to the internal organization.
Of course, all calculations are then discussed with the management. And the warehouse workers will be well informed and involved, because their jobs will undergo a change.
But don’t forget that a new automated warehouse has an impact on the entire organization. Purchasing, marketing, production; they all play a role in the goods receipt and issue process. Ensure a good exchange of information or involve these departments in putting together the project team.
The last pitfall is not in the preparation, but is an assumption.
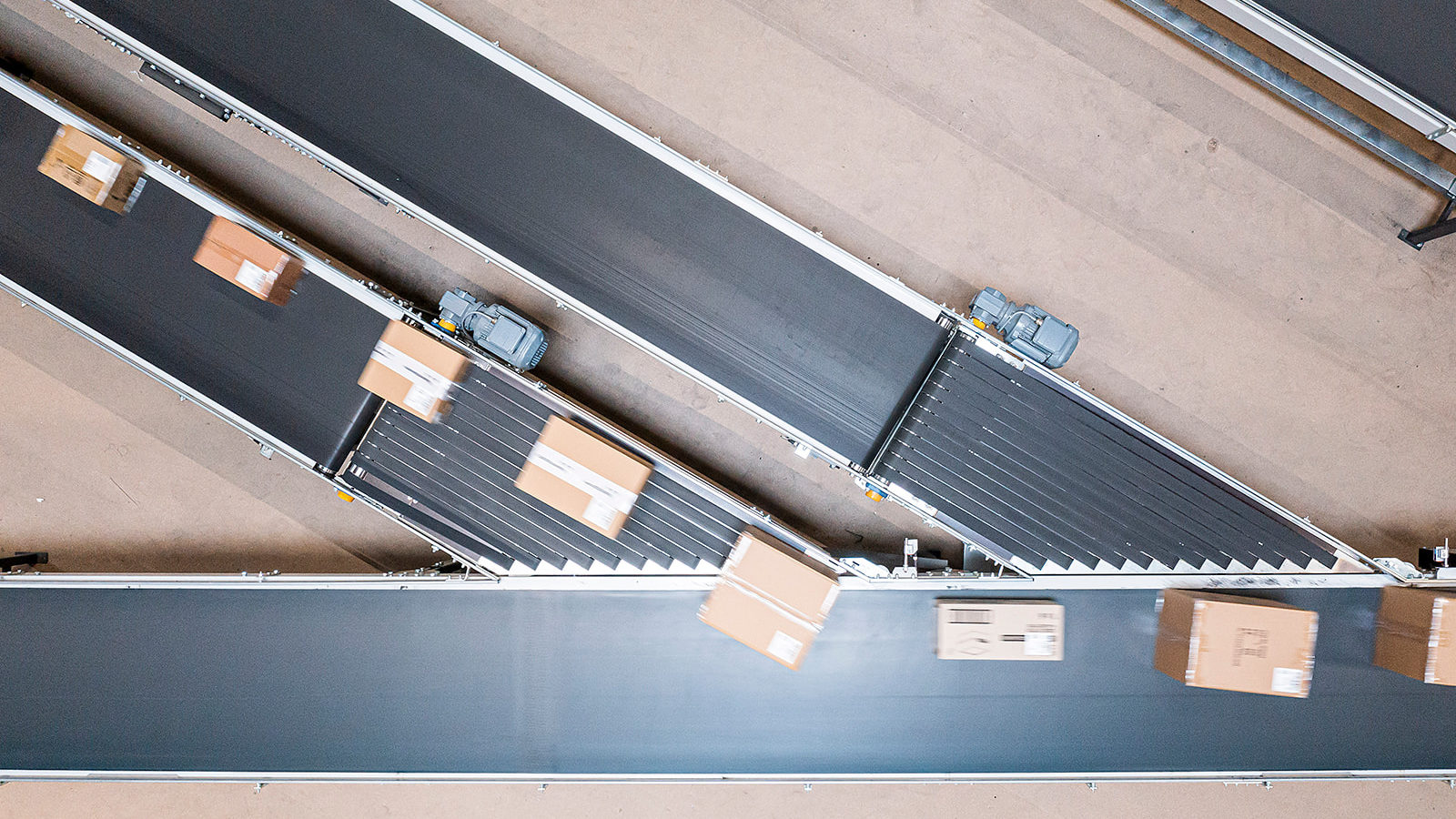
The automated system is often too rigid.
The words automation or mechanization give some companies visions of rigid high-bay warehouses with cranes doing the same trick day in and day out for ten or fifteen years. But who can look that far ahead? Who dares to predict what his demand and his order pattern will look like in five years?
The idea that automatic warehouse systems are by definition rigid systems and difficult to scale is no longer true. The market has increasingly flexible forms of automation. Think of zone picking systems with smart conveyors in combination with conventional shelf racks that make it possible to achieve large profits in the order picking process. Not to mention the ergonomic benefits. Or think of shuttle systems where the number of shuttles can grow with market demand.
Let’s go back to the beginning of this blog. It is about a good analysis of the warehouse. Now and in the future. Some processes can be well standardized and can therefore make great gains with automation. But bulk storage remains bulk storage and, for example, the good old drive-in rack may suffice.
Automating a warehouse requires the necessary calculations and preparation, but can also yield major benefits afterwards.
COSTO Intralogistics expertise in practice.
Get inspired by one of our other projects!
Service and Support
Subscribe to our newsletter.
"*" indicates required fields