Automation issue in your warehouse?
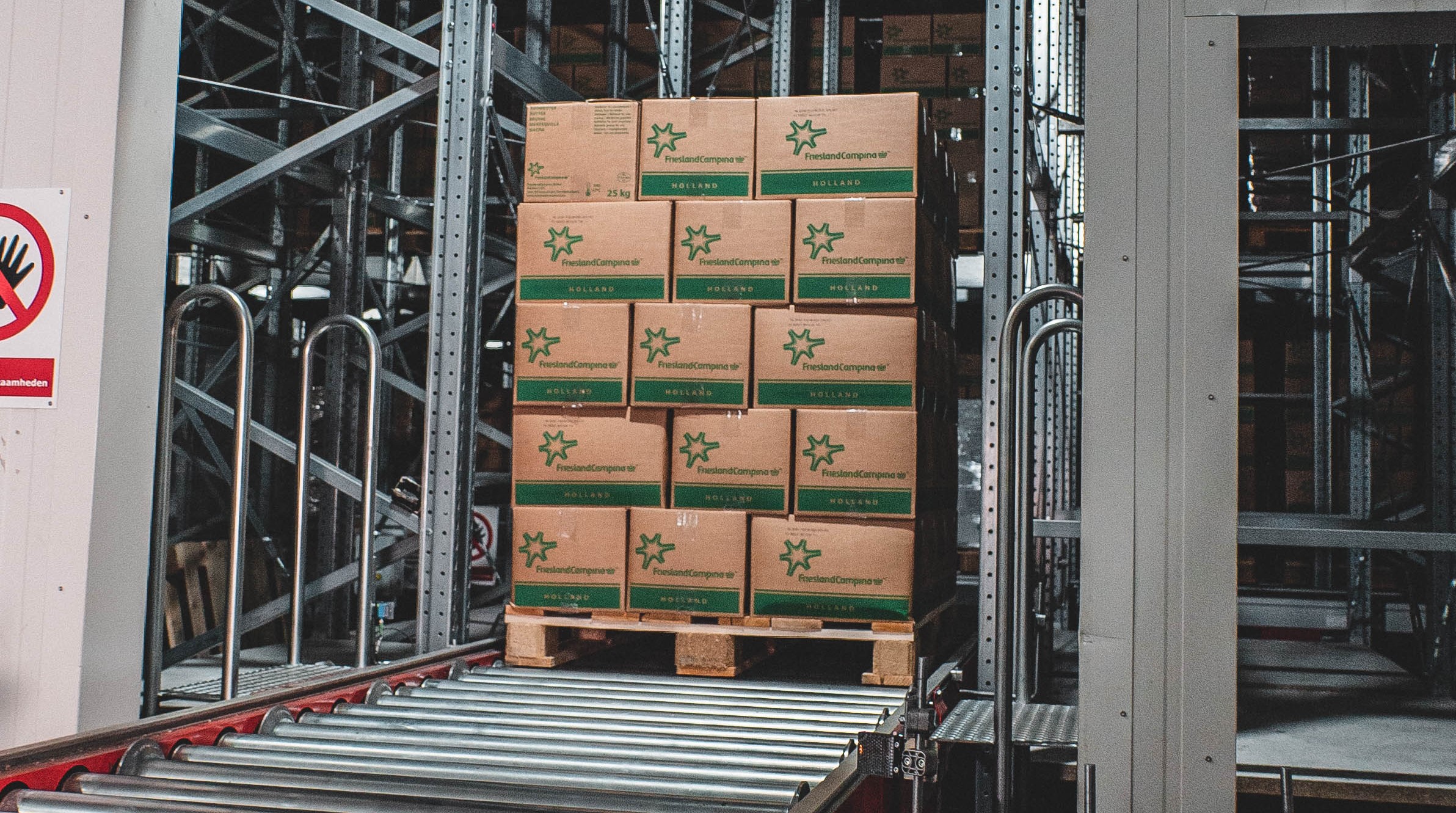
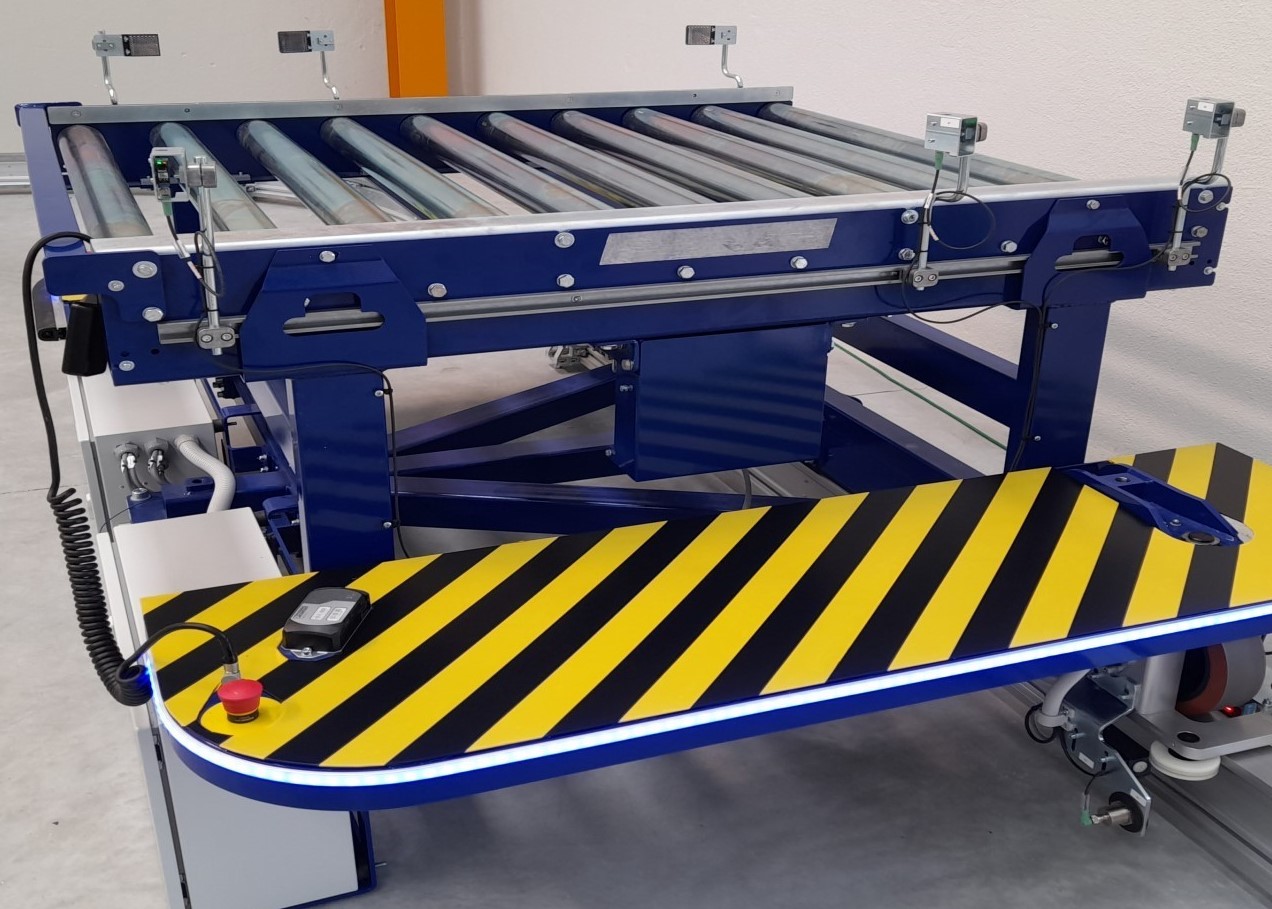
The conveyor
We often see the conveyor with driven rollers used for pallets. The choice for this system is mainly a practical one; the technology has more than proven itself, the installation is relatively simple and there are no exceptional requirements with regard to the floor. It is pre-eminently a system for shorter distances and for transporting pallets up to a certain weight from A to B. In terms of investments, the system will satisfy the corporate accountant, who are relatively friendly.
However, there are also a number of drawbacks to the conveyor: the fixed set-up can form an obstacle for personnel or other internal transport equipment, so careful thought must be given to the route. It also costs time (= money) to adjust the installation later and the solution may be less suitable for frequently changing situations (think of lean manufacturing or warehouses with a “continuous improvement” philosophy). In addition, maintenance downtime must be taken into account. The roller conveyor cannot then be used. The scalability is also limited, although disassembly and reassembly are a lot easier with the modern, modular variants.
The AGV
Choosing the AGV means choosing an automated transport system with unmanned vehicles. They are extremely suitable for short and medium-long transport of pallets from A to B. Because the AGV does not need any rails or other obstacles and it “knows” where it needs to be, productivity can be significantly increased with this system. In addition, routes can be easily modified. The longer you use the AGV, the bigger the profit of course. That is why the AGV is ideal in multi-shift situations or in environments where a certain flexibility is desired. During maintenance, only the concerning AGV sits on the reserve bench for a while, while the other vehicles continue to do their job. Improved continuity is therefore one of the advantages of an AGV set-up. We see AGVs a lot in the paper industry, the automotive industry or production companies, but in the meantime they can be used more and more in all kinds of warehousing applications.
However, the AGV cannot be used everywhere. For example, the floor must be completely flat and the relatively high investment does not always make a justifiable payback period possible. So it all depends on the application.
RGV; the golden mean?
An RGV is a transport system with vehicles on rails. The vehicles can often pick up the pallet themselves. Usually an RGV system is mounted on the floor, but a hanging variant is also possible. Due to the high speeds (above 3 meters per second!) large distances can be covered quickly. In addition, the pallet loads can be much heavier than with the standard conveyor or AGV: up to 10,000 kg! As with the AGV, only the vehicle in question needs to be removed from the process during maintenance, while the rest ‘continues to work’.
An RGV also has its downsides: just like the conveyor, it is a fixed set-up and adjustments are not always easy. Moreover, the investment is usually slightly above that of a conventional roller conveyor.
Can we call the RGV a golden mean? No, that is also not the case. As cliché as it sounds; it depends on your processes which system scores best.
Costo will be happy to visit you to discuss your wishes and to determine the optimal configuration. Call us today: 0183-745045!
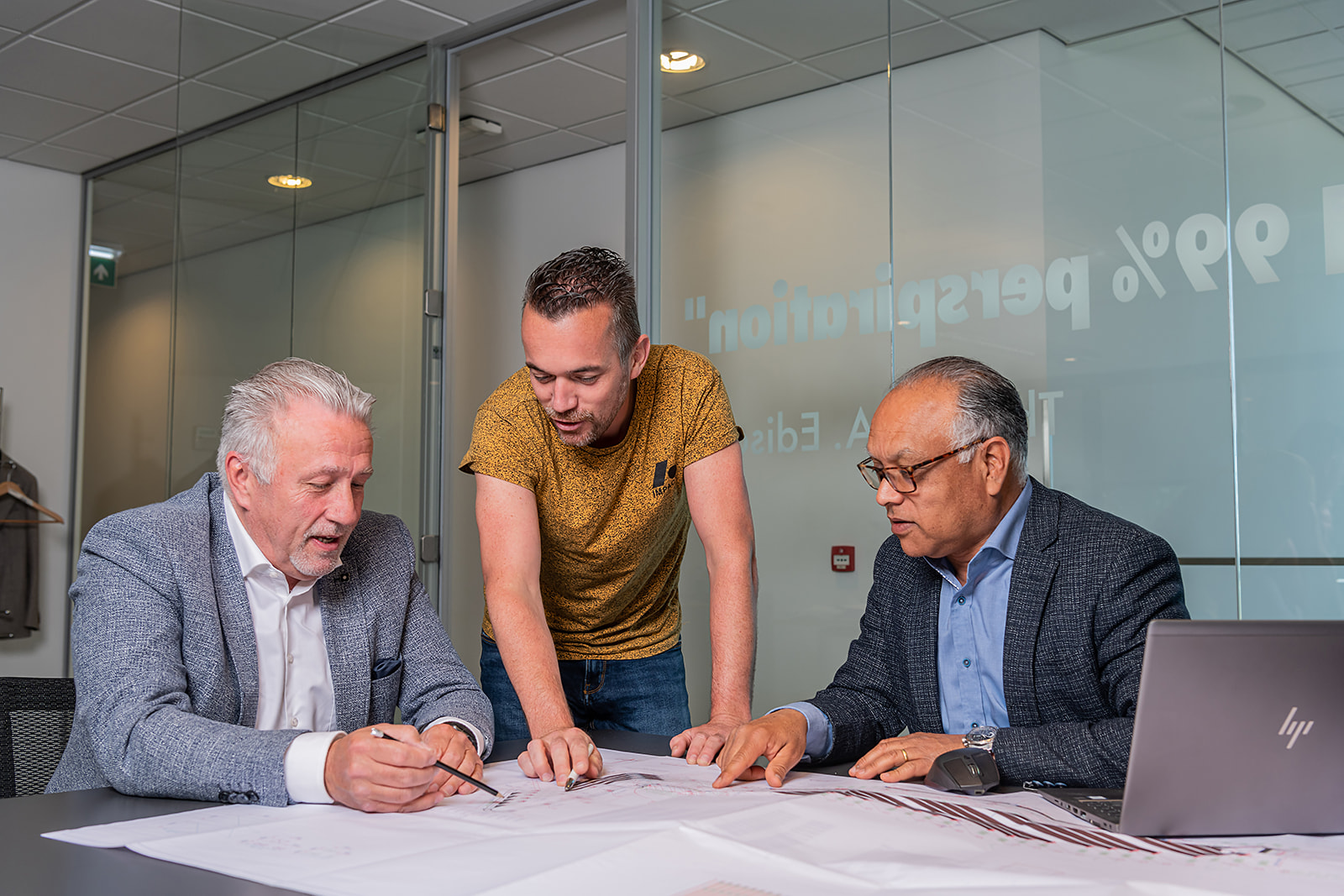
Advice
Feel free to contact our specialists
Do you want advice about the automation of your warehouse? Feel free to contact us.
Our experienced team will be glad the help you!